I've been weeding along the fences where the graders did not get the weeds. They didn't get to these weeds because there were things in their way, like the water tanks and materials I have been collecting. I also did a little site cleanup, though the workers were pretty good at cleaning up after themselves. One issue I'll have to address with their bosses is the trash disposal. While my trash bin was empty, they had put their plastic bags of trash in both my green bin and recycle bin. Being the recycling addict I am, I went through every bag and separated the trash into its proper bin. Fortunately much of it could go in the green bin as our trash collection company is now collecting compostable things like soiled paper and food waste!!
![]() |
My son and cameraman |
This gives you an idea of the enormity of this facility, but shows only a part of it. |
James, Mike and Adrian answering my questions and explaining how it all works. |
James with me inside half my downstairs living space |
Lowering a container to look inside to check the flooring. |
Most often, shipping container floors are 1 1/8" marine plywood made from tropical hardwood such as Keruing or Apitong. These floors are often treated with pesticides so it is recommended to seal them. I assumed this was done before applying your choice of flooring, but James pointed out that there is another option--using the existing floor as the finished floor. The 40' containers have a metal plate in the floor at one end which wasn't particularly attractive, but the 20' container floors were all wood. The containers we looked at had 3 different types of floors. One was a dark laminate that wasn't particularly attractive. One was a bamboo floor but it was stained red. The third was Apitong, if I remember correctly. We liked the look of it and I decided it would be a good option for the ADU, but James and Mike have to see if they can locate two 20s with that floor. If they can get the containers, they will sand the floor and seal it with Epoxy. I had said that the greenest floor was reclaimed wood, but using the existing wood would be even better.
Apitong |
Red Bamboo |
Laminate |
![]() |
James arranged for some fireworks for us while we were there. Sparks fly when the metal is being cut. |
Here Adrian is using a plasma cutter to cut an opening in one of the containers. |
![]() |
![]() |
It was quieter than I expected, but did smell. |
The plasma cutter made quick work of the opening. This will be the opening for the sliding glass door off of the downstairs bedroom.
|
That was the end of our tour. I got all my questions answered and can't wait to go again to see the progress.
On the way home we stopped at Urban Ore in Berkeley to check out their materials. It is a giant thrift store for building supplies, as well as some clothing, kitchenware, records and books, etc. They have hundreds, if not thousands, of doors. It wouldn't be easy to sort through them to find what you need. Their kitchen cabinets weren't as nice as those at Habitat for Humanity's Restore in Redwood City, but I'm sure their inventory is constantly changing. I wasn't expecting to buy anything--we were just getting a feel for what they have. Danny did find a large hooded fur coat he liked and he bought it for Burning Man.
Friday morning the surveyors came to set markers for the foundation crew to work from. They have better equipment and expertise to more accurately mark the building corners and elevations. Juno is enjoying her modified space.
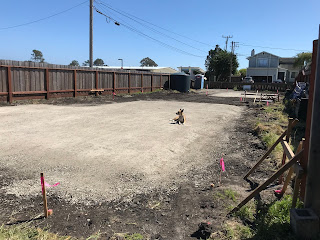

While the surveyors did their work, I was attending a webinar through the PG&E Energy Center. Whatever you may think of PG&E, they have excellent educational programs for both professionals and homeowners. Many of the courses are held in San Francisco, but some of them are also available online or on demand. This class was on Integrated Design Thinking for Net Zero Energy Residential Buildings. It is a mouthful, but really says it all. All new homes in California will have to be NZE soon. The class was about how to do this efficiently and without adding a lot of additional expenses to the project. One of the best things you can do is to spend more time in the design phase, utilizing the expertise of the various trades in a collaborative way. A common way to build is more a sequential series of events. An architect and homeowner come up with a design. They take it to a structural engineer, then it goes to an energy engineer before going to the building department for a building permit. Once a permit is obtained, a contractor is hired to build it. The contractor in turn hires sub-contractors to do the HVAC, foundation, framing, finishes, etc. With a collaborative approach you get all these people together during the design phase. For example, to save money they might figure out a way to spend more on insulation that could save on the size of the heating and cooling systems. The design phase takes longer, but the construction time is reduced because there are fewer changes. Other suggestions include simplifying the design (such as roof lines), smaller size and fewer windows.
While I didn't have the collaborative design in my project, I will make it a requirement on anything I do in the future.
Here is a great lecture on the subject with an emphasis on affordability:
https://www.youtube.com/watch?v=KvJWCLYqAnA&feature=youtu.be
And here is a written guide authored by the PG&E instructor:
https://energycodeace.adobeconnect.com/aia-zne-guide/
We are expecting to get the plans back from the city this week, otherwise we won't be doing much on site, however, nothing is stopping James and his team with moving forward with the containers.